Глава 6. Конструкция перегонного аппарата
Все детали перегонного аппарата, за исключением стеклянного манометра, резиновых и фторопластовых прокладок, изготовлены из нержавеющей стали. Этот выбор сделан осознанно, несмотря на то, что со средних веков и вплоть до настоящего времени на родине получения виноградных спиртов во Франции используются перегонные аппараты-дистилляторы только шарантского (по названию провинции) типа, изготовленные исключительно из красной меди — т.н. аламбики. Их конструкция и размеры основных частей — куба, шлема (колпака), пароотводной трубки, змеевикового холодильника и бака с охлаждающей водой — строго регламентированы. Использование нержавеющей стали, лужёной меди или стекла в производстве коньячных спиртов не допускается [27].
Дело в том, что первоначально опытным путём было выяснено, что невысокого качества виноградный спирт, полученный перегонкой на дистилляторе с медным кубом и длительное время выдержанный в дубовой бочке, обладает лучшими органолептическими характеристиками, чем спирты, перегнанные в аппаратах из стекла или железа.
Позднее, по мере развития химии было установлено, что медь является весьма активным элементом. Она участвует как один из реагентов и как катализатор в реакциях между различными химически активными веществами, кипящими в кубе перегонного аппарата. Например, при изготовлении коньячного спирта в аппарате с медным кубом образуется эфиров на 60—100% больше, альдегидов на 10—15%, фурфурола на 150—200% больше, чем в аппаратах с кубом, лужёным серебром или оловом [76]. То есть, медь способствует образованию новых летучих веществ, зачастую ядовитых, которые только после многолетней выдержки в дубовых бочках и взаимных превращений с участием кислорода улучшают вкус коньяка, но их употребление внутрь непосредственно после перегонки причиняет вред здоровью. Это, прежде всего, относится к фурфуролу, альдегидам и эфирам, содержание которых в спирте, полученном перегонкой из медного куба, значительно выше, чем в спирте, перегнанном в кубе из стекла или лужёной меди [27].
Кроме того, в присутствии воды и углекислого газа, которого более чем достаточно в виноматериале особенно при первой перегонке, на поверхности меди и её сплавов образуется патина — плёнка зеленоватого цвета, состоящая из ядовитой углекислой соли меди. То, что плёнка патины нерастворима в воде, служит слабым утешением, поскольку при достаточно толстом слое возможно её шелушение и попадание в отгоняемую жидкость.
Медь, правда, способствует связыванию сернистых соединений, если они присутствуют в дистилляте после первой перегонки и придают ему тухлый запах [69], но в результате на поверхности медных частей перегонного аппарата, например, внутри змеевикового холодильника, образуется рыхлый налёт тёмного цвета, содержащий серу. На последних этапах перегонки частицы этого налёта отваливаются и попадают в дистиллят.
Есть также сообщения [39], что продукты перегонки в медных аппаратах при застаивании в них бродильной жидкости приобретают запах сероводорода. То же относится и к содержащему серу чугуну.
Поэтому наиболее подходящим материалом для изготовления перегонного аппарата, с учётом требований по надёжности и пожаробезопасности, является пищевая нержавеющая сталь.
Поперечное сечение и внешний вид головной части перегонного аппарата, разработанного с учётом всех перечисленных выводов и рекомендаций, приведены на рис.7 а и рис.7 б. Рисунки выполнены не в масштабе, чтобы проще было уяснить назначение и работу основных частей устройства в процессе перегонки.
Аппарат состоит из куба 1 — цилиндрической ёмкости с плоским дном общим объёмом около 14 л и полезным — 10 л. Внутренняя поверхность дна и прилегающие к ней вертикальные стенки на высо3—4 см подвергнуты пескоструйной обработке. Это придаёт поверхности шероховатость, которая по описанным выше соображениям способствует адсорбции на ней центров парообразования и установлению благоприятного режима пузырчатого кипения.
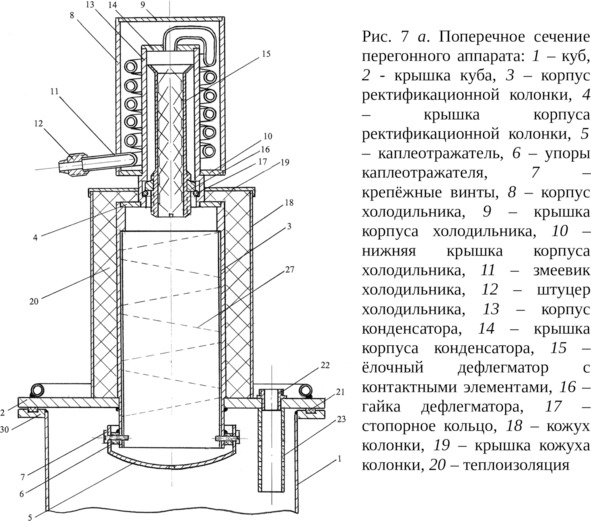
Увеличение объёма куба свыше 10 литров представляется нецелесообразным, т.к. при забраживании виноматериала в стандартной 20-ти литровой стеклянной бутыли она перегоняется на первой перегонке за 2 процесса — по 10 литров в каждом. При этом выход продукта после первой перегонки с одной бутыли составляет примерно 2,6—3,1 литра. Таким образом, на вторую перегонку поступает около 6,5—7,0 литров, полученных при первой перегонке 2-х бутылей, что позволяет оптимально использовать объём аппарата на 2-ой и, если потребуется, 3-ей перегонках. Кроме того, например, 30-ти литровый куб перегоняется в три раза дольше 10-ти литрового, а фактически ещё дольше, т.к. у него больше излучающая тепло поверхность. Но чем дольше развариваются дрожжи, тем больше в кубе образуется вредных альдегидов и высших спиртов. Производители коньячных спиртов специально затягивают процесс 1-ой перегонки, да ещё добавляют в куб воду, чтобы увеличить выход высших спиртов.
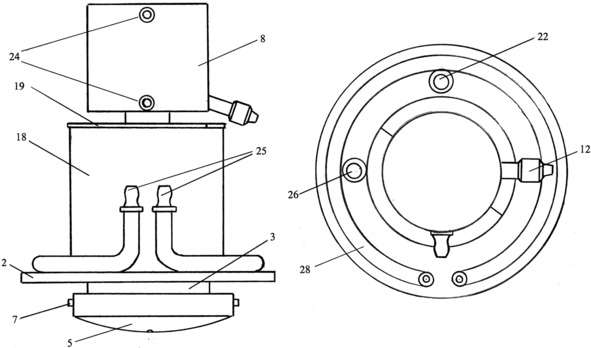
Рис. 7 б. Внешний вид головной части перегонного аппарата:21 — резиновая прокладка, 22 — ввод манометра, 23 — экран манометра, 24 — штуцеры подвода воды к холодильнику, 25 — штуцеры трубки охлаждения прокладки, 26- ввод термометра, 27 — сетки ректификационной колонки (элементы крепления сеток не показаны), 28 — трубка охлаждения прокладки, 30 — фланец куба.
Фото 1. Внешний вид собранного перегонного аппарата.
К верхней части куба аргонно-дуговой сваркой приварен фланец 30 с проточкой под уплотнительную резиновую прокладку толщиной 4,5—5,0 мм. Если прокладка изготавливается из листовой резины, то её необходимо притереть. Для этого лист толстого — 5—8 мм стекла с размером больше диаметра прокладки оборачивают без складок листом мелкозернистой шкурки по дереву. Прокладку вставляют с натягом в проточку во фланце, тщательно прижимают к фланцу и шлифуют листом стекла со шкуркой, поворачивая его вокруг вертикальной оси куба туда-сюда. Притирку проводят до тех пор, пока на всей поверхности прокладки не останется не зашкуренных участков. Затем прокладку вынимают, переворачивают и проводят притирку обратной стороны. Притирка прокладки позволяет значительно уменьшить усилие прижима фланца к крышке куба для обеспечения герметичности соединения. Чтобы прокладка меньше нагревалась в процессе перегонки, сверху на крышку куба 2 наварена трубка охлаждения 28, согнутая в кольцо с диаметром, приблизительно равным диаметру проточки под прокладку во фланце 30.
На концы трубки охлаждения 28 наварены штуцеры 25, на которые надеваются резиновые шланги подачи воды. Вода из водопроводной системы сначала поступает в нижний штуцер 24, вваренный в корпус холодильника 8. Верхний штуцер холодильника соединяется резиновой трубкой с одним из концов трубки охлаждения 28. Пройдя снизу вверх через холодильник, а затем через трубку охлаждения прокладки, вода из второго штуцера 25 поступает по шлангу в слив.
В крышку куба 2 вварены ввод манометра 22 и ввод термометра 26. С нижней стороны крышки на ввод манометра наварена металлическая трубка-экран 23. Экран защищает стеклянную трубку манометра от разрушения при случайных ударах, когда головная часть аппарата снимается по окончании перегонки содержимого куба. На горловину ввода термометра, в случаях, когда он в силу каких-либо причин не устанавливается, навинчивается крышка 26—1, уплотнённая фторопластовой прокладкой 26—2. Корпус термометра уплотняется в месте ввода в крышку резиновой конусообразной пробкой, которая вынимается из ввода вместе с термометром при манипуляциях с головной частью аппарата. Термометр должен быть рассчитан на измерение температуры не менее 100оС.
В центр крышки куба 2 вварен корпус 3 ректификационной колонки, в который вставляется съёмная колонка с сетками 27. Сверху на корпус колонки наварена крышка 4 с отверстием для ввода корпуса конденсатора 13. Нижняя часть корпуса колонки закрывается каплеотражателем 5, который привинчивается к нему винтами 7 через три упора 6, обеспечивающих необходимый зазор между стенками каплеотражателя и корпусом колонки. Для того, чтобы стекающий из ко-
лонки конденсат не скапливался в каплеотражателе, последний имеет вогнутое дно с дренажным отверстием в центре.
Корпус колонки имеет кожух 18, закрытый крышкой 19, которые изготовлены из тонкой листовой нержавеющей стали. Внутреннее пространство между кожухом и корпусом колонки заполнено теплоизолятором — шариками пенополистирола от упаковочной тары. Кожух заполняется теплоизолятором и закрывается разрезной крышкой после сварки всех остальных частей аппарата. Поскольку кожух и крышка не контактируют со спиртосодержащими парами, они взаимно соединяются обычной пайкой с припоем ПОС. Предварительно места пайки залуживают с использованием не особенно опасной в обращении ортофосфорной кислоты. Надёжная термоизоляция колонки является необходимым условием её правильной работы, т.к. даже незначительное и тем более неравномерное охлаждение наружных стенок колонки, например, сквозняком из окна может привести к нарушению протекающих в ней процессов тепло- и массообмена. Внешне это проявляется или срывом тонкой струйки вытекающего из аппарата дистиллята на капли или полной остановкой процесса перегонки.
В центральное отверстие в крышке корпуса колонки 4 вварен корпус конденсатора 13 с крышкой 14. Через отверстие в крышке спиртосодержащие пары поступают в змеевиковый холодильник 11. Он представляет собой трубку из нержавеющей стали, разогретую на газовой горелке и согнутую в спираль на цилиндрической деревянной оправке подходящего диаметра. Шести витков змеевика вполне достаточно для полной конденсации паров спирта при температуре охлаждающей воды 9—18оС и её расходе ~ 1,0 л / мин. При более высокой температуре водопроводной воды можно просто увеличить её расход. Но в этом нет особенной необходимости, поскольку при сборе урожая винограда в конце сентября — начале октября, его переработка в виноматериал заканчивается в середине ноября, а к этому времени температура воды в водопроводе опускается ниже 18оС.
Для надёжного соединения выхода холодильника с резиновой трубкой, по которой дистиллят стекает в приёмную ёмкость, на конец змеевика наварен специальный штуцер 12. Во избежание самопроизвольного соскакивания резиновой трубки со штуцера и возникновения пожара, в конструкции штуцера предусмотрены шайба 12—2 с внутренним диаметром, равным наружному диаметру резиновой трубки, и накидная гайка 12—1 (см. приложение 1). При сборке данного узла на резиновую трубку сначала надеваются накидная гайка и шайба. Затем конец трубки натягивается на конусообразную часть штуцера 12 и закрепляется на нём при навинчивании накидной гайки, которая надвигает шайбу на конус штуцера и надёжно фиксирует резиновую трубку. Второй конец трубки пропускается через отверстие в бытовой капроновой крышке, надеваемой на обычную трёхлитровую банку — приёмную ёмкость. Трубка вставляется в отверстие в крышке со значительным натягом и пропускается на длину 3—4 см. Для выхода вытесняемого дистиллятом из приёмной банки воздуха в её крышке пробивают второе отверстие диаметром 3мм. Сама крышка должна надеваться на банку достаточно плотно, чтобы исключить случайное соскакивание, но не настолько туго, чтобы для её снятия нужно было прилагать чрезмерные усилия. Это может привести к опрокидыванию банки или расплёскиванию содержимого.
Приёмную банку полезно отградуировать через 0,1 литра при помощи мерной ёмкости и тонких полосок липкой изоляционной ленты. Это позволит не только сравнивать между собой результаты различных перегонок, но и контролировать наличие гарантированного остатка жидкости в кубе по разности залитого и перегнанного объёмов. Из двух типов выпускаемых промышленностью банок лучше выбрать не «пузатую», а ту, что постройнее — выше будет точность градуировки. Разумеется, что банка должна быть из прозрачного белого стекла.
В качестве резиновой трубки, соединяющей выходной штуцер аппарата с приёмной банкой, необходимо использовать прозрачную трубку из силиконовой резины. Трубка должна иметь постоянный наклон в сторону от выходного штуцера аппарата к крышке приёмной банки, чтобы в ней не скапливался дистиллят и, как следствие, не возникало избыточное давление в кубе. Минимальная длина трубки должна быть такой, чтобы при случайном срыве крышки она не попала на газовую горелку, а была ниже неё на 15—20 см. Не стоит также делать трубку излишне длинной и не помещать приёмную банку на неустойчивую опору, например, табурет. Впрочем, высоты аппарата вполне достаточно для размещения банки на кухонном столе или тумбе рядом с газовой плитой.
Головная часть перегонного аппарата, установленная на фланец куба 30 с прокладкой 21, прижимается к нему шестью съёмными подпружиненными зажимами 29 (см. приложение 1), расположенными примерно через 60о по длине окружности крышки куба. Практика показала, что такая конструкция подпружиненных зажимов обеспечивает плотное прилегание крышки к прокладке и исключает деформацию фланца, к которому приварена достаточно тонкая стенка куба. При использовании зажимов в виде традиционных струбцин возможна деформация фланца при их неравномерном затягивании, как следствие, возникновение трещины в сварном шве стенки куба.
Крайне важной частью аппарата является манометр. Он изготавливается из термостойкой стеклянной трубки диаметром 10 мм. Трубка изогнута так, как показано на рис.8 и имеет шарообразное расширение на верхнем конце. Нижним концом трубка манометра вставляется в ввод манометра в крышке куба и надёжно фиксируется в нём при помощи накидной гайки 22—1, направляющей втулки 22—2 и резиновой прокладки 22—3, зажимаемой между конусными стенками втулки и ввода манометра. В результате прокладка деформируется и надёжно уплотняет зазор между сопрягаемыми деталями. Но при необходимости манометр может быть установлен также как и термометр при помощи конусообразной резиновой или корковой пробки, показанной на рис. 8.
Внутрь манометра примерно до половины высоты центральной трубки наливается обыкновенная вода. Если по какой-либо причине давление в кубе возрастёт, столбик воды в центральной трубке манометра опустится, а в соседней с ней правой соответственно поднимется. Избыточное по отношению к атмосферному давление в нормально работающем аппарате редко поднимается выше 10—15 мм водяного столба, но при случайных толчках в кубе возможно выплёскивание воды из манометра. Чтобы исключить выплёскивание, на конце верхней части манометра предусмотрено шарообразное расширение. Поднимающаяся при увеличении давления вода достигает шарика и начинает заполнять его объём. При этом скорость подъёма жидкости в вертикальном направлении существенно уменьшается, что предотвращает её выплёскивание из манометра. При уменьшении давления в кубе жидкость из шарика стекает обратно в U-образную трубку.
Манометр выполняет три важные функции. Во-первых, он измеряет собственно давление пара в кубе и позволяет вовремя остановить процесс перегонки, если давление становится подозрительно высоким. Например, в случае, когда перед заливкой в аппарат виноматериал не был тщательно отцежен, и кожица винограда забила входное отверстие в холодильнике. Во-вторых, манометр служит своего рода предохранительным клапаном — при неожиданно резком повышении давления вся жидкость из манометра будет вытолкнута наружу и избыток пара выйдет через манометр как через отводную трубку.
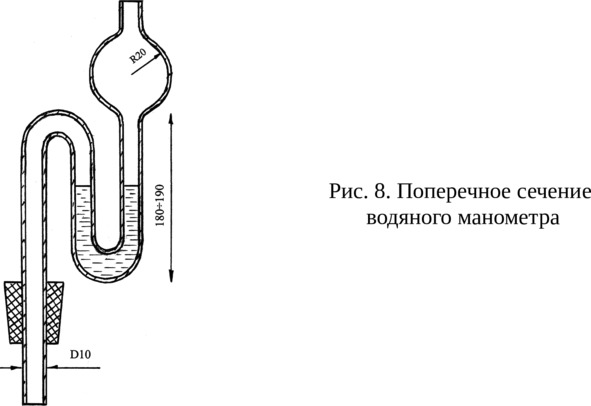
В-третьих, при излишне интенсивном нагреве куба колонка может «захлебнуться» флегмой (или забиться интенсивно образующейся пеной) и на некоторое время потерять пропускную способность. Эту ситуацию можно отследить по увеличению общего количества жидкости в манометре из-за конденсации поступающего в него пара. В этом случае нагрев куба нужно уменьшить или полностью прекратить перегонку до осаждения пены. Конструкцию манометра при желании можно упростить, оставив стеклянной только часть трубки с шариком, а остальное — изготовить из нержавеющей трубки диаметром 10 мм. Состыковать стеклянную и металлическую часть манометра можно при помощи отрезка из силиконовой трубки подходящего диаметра.
Основным конструктивным элементом перегонного аппарата, обеспечивающим эффективное разделение спиртосодержащих смесей, является ёлочный дефлегматор 15, в котором установлены восемь контактных элементов (поз.15—1 приложения 1).
Контактные элементы изготавливаются следующим образом. Сначала из тонкого плотного картона вырезается указанных размеров лекало. Затем по нему расчерчиваются и вырезаются из листовой нержавеющей стали толщиной 0,3 мм 8 шт. плоских заготовок. На металлической трубке или цилиндре с диаметром несколько большим внутреннего диаметра корпуса дефлегматора заготовки сворачиваются в кольцо, а затем четыре острия с каждой стороны отгибаются к центру. Далее контактные элементы поочерёдно вставляются внутрь корпуса дефлегматора, при этом каждый последующий элемент поворачивается относительно предыдущего примерно на 45о, так чтобы иглы одного находились между иглами другого, а иглы двух соседних элементов заходили друг за друга и сходились в их центральной части.
При изготовлении контактных элементов и их установке в корпус дефлегматора необходимо осуществить по возможности наиболее плотное прилегание кольцевой центральной части каждого контактного элемента к внутренней поверхности корпуса дефлегматора для обеспечения хорошего теплового контакта. Только в этом случае в дефлегматоре будет иметь место так называемая противоточная дефлегмация, когда спиртосодержащие пары, поднимаясь вверх, частично конденсируются на концах игл. Конденсат (флегма) непрерывно стекает по обращённым вверх иглам к более холодной стенке дефлегматора, а с неё попадает на концы игл, обращённых вниз, где вновь разогревается поднимающимся из куба горячим паром. Остаток прошедших через дефлегматор паров, не сконденсировавшихся на иглах, попадает в холодильник. В результате достигается большое обогащение дистиллята низкокипящим компонентом (спиртом), т.к. при частичной конденсации (дефлегмации) спиртосодержащих паров преимущественно конденсируются высококипящие компоненты. Кроме того, поднимающийся навстречу флегме горячий пар многократно контактирует с ней на иглах дефлегматора, что способствует наиболее полному удалению из флегмы низкокипящего компонента.
Игольчатая конструкция дефлегматора выбрана не случайно. Предварительно были опробованы дефлегматоры тех же размеров, но не заполненные ничем (пустая трубка) или заполненные разрезными 4-х миллиметровыми кольцами из нихромовой проволоки толщиной 0,3 мм. Дефлегматоры были ввёрнуты в корпус конденсора до упора в его крышку. Во всех случаях при одной и той же интенсивности нагрева разгонялось по 5 литров водно-спиртовой смеси, содержащей 10% спирта. Перегонка проводилась до получения одного и того же количества дистиллята, который затем подвергался повторной перегонке. Во всех случаях — по концентрации спирта в отгоне и скорости перегонки ёлочный дефлегматор имел преимущество. Например, скорость отбора дистиллята на первой перегонке у него составляла 31,8 мл/мин по сравнению с 29,1 мл/мин у дефлегматора, заполненного кольцами, и 27,6 мл/мин у пустого. На второй перегонке это преимущество возрастало: 38,2 мл/мин у ёлочного и 30,4 мл/мин у дефлегматора с кольцами.
Как было отмечено выше, эффективность работы дефлегматора и расположенной под ним ректификационной колонки существенно повышается, если часть сконденсировавшихся паров принудительно возвращается назад, орошая колонку и дефлегматор. Для этой цели в конструкции перегонного аппарата предусмотрен конденсатор, состоящий из собственно корпуса 13 и верхней воронкообразной части корпуса дефлегматора 15. Снаружи корпус конденсатора охлаждается проточной водой, которая стабилизирует его температуру. Воронкообразная часть дефлегматора тщательно притёрта на абразивной пасте к внутренней поверхности корпуса конденсатора, для того чтобы образующийся конденсат стекал внутрь дефлегматора, а не по стенке конденсатора. Объём возвращаемого в дефлегматор конденсата регулируется путём перемещения дефлегматора в корпусе конденсатора по вертикальной оси. Для этого предусмотрена гайка 16, удерживаемая в корпусе конденсора стопорным кольцом 17 (чертёж на эту деталь в приложении 1 не приводится ввиду её очевидной простоты). При вворачивании дефлегматора из крайнего нижнего положения вверх уменьшается площадь внутренней поверхности конденсатора, заключённого между его крышкой и воронкообразной частью дефлегматора, на которой происходит конденсация паров. Соответственно уменьшается и количество возвращаемого в дефлегматор конденсата. Когда дефлегматор ввинчен в корпус конденсатора до упора, орошение будет минимальным, а максимальное орошение достигается при максимально вывинченном дефлегматоре.
Параметры перегонки в зависимости от положения ёлочного дефлегматора в конденсаторе приведены в таблице 1. Во всех случаях при одной и той же интенсивности нагрева разгонялось по 4 литра водно-спиртовой смеси, оставшейся при отделении головных и хвостовых частей дистиллята при предыдущих перегонках.
Таблица 1
Содержание спирта в смеси определялось по бытовому спиртометру со шкалой от 5 до 96о.
Из приведённых данных следует, что с увеличением орошения (дефлегматор вывинчивается из корпуса конденсатора с 4 мм до 28,5 мм) скорость перегонки уменьшается, что влечёт за собой увеличение её длительности более чем в 1,5 раза. Однако, разделение смеси на спирт и воду происходит с большей эффективностью — содержание спирта дистилляте при максимальном орошении на 29,4% выше, чем при минимальном (при расчёте содержания спирта использовалось правило смешения из приложения 3). Исходя из полученных данных, было выбрано компромиссное с точки зрения скорости перегонки и эффективности разделения смеси положение дефлегматора в корпусе конденсора, равное 15 мм. Этот размер оставался неизменным практически во всей дальнейшей работе.
В таблице 2 приведены параметры перегонок, проведённых в описанных выше условиях, с использованием ёлочного дефлегматора и дефлегматора с нихромовыми кольцами при наличии орошения. Для этого дефлегматоры были вывернуты из корпуса конденсора на одно и то же расстояние, равное 15 мм.
Таблица 2
Из таблицы 2 видно, что при наличии орошения применение ёлочного дефлегматора также позволяет получить лучший результат по эффективности разделения водно-спиртовой смеси, чем у дефлегматора с кольцами и существенно (в 1,3 раза) повысить содержание спирта в дистилляте.
Увеличение длины дефлегматора на 150 мм при том же орошении не привело к заметному улучшению качества дистиллята, но потребовало заметного увеличения интенсивности нагрева куба.
Ещё одним важнейшим элементом конструкции перегонного аппарата является ректификационная колонка, поперечное сечение которой приведено на рис. 9. Колонка изготовлена в виде отдельной съёмной конструкции, чтобы её можно было достаточно легко извлечь из корпуса в аппарате перед проведением первой перегонки. Дело в том, что подготовленный к перегонке виноматериал содержит большое количество коллоидных частиц и легко вспенивается при неправильно выбранной интенсивности нагрева куба. Пена забивает нижнюю часть колонки, движение пара в ней прекращается, давление в кубе резко возрастает и происходит аварийный выброс жидкости из трубки манометра.
Колонка представляет собой цилиндр 1 из листовой нержавеющей стали толщиной 0,5 мм. Цилиндр отформован путём прокатки на вальцах под заданный диаметр плоской заготовки нужного размера. Точечной контактной сваркой стык цилиндра сваривается в 6—8 местах, в том числе на расстоянии 6—7 мм от краёв. Кромка верхней части цилиндра по всей окружности отбортована внутрь, что препятствует выпадению из него элементов крепления сеток. Нижняя кромка цилиндра также по всей окружности отбортована наружу, что в случае необходимости облегчает извлечение колонки из её корпуса в аппарате (рис. 7а-3). В нижней части цилиндр имеет три отверстия диаметром 4 мм, соосные упорам каплеотражателя (рис. 7а-6). Крепёжные винты каплеотражателя (рис. 7а-7) вворачиваются в упоры и далее проходят сквозь отверстия в цилиндре колонки, обеспечивая тем самым надёжное крепление колонки в корпусе.
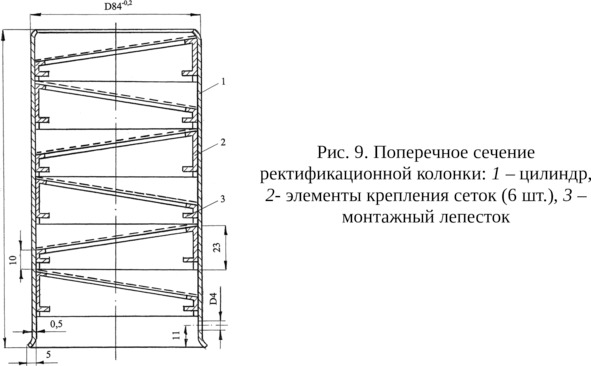
В качестве контактного элемента в колонке использована изготовленная промышленным путём сетка из нержавеющей проволоки диаметром 0,1 мм и, по-видимому, с размером ячеи 0,1 х 0,1 мм2. Шесть штук таких плоских сеток приварены контактной сваркой к элементам крепления 2. Элементы крепления изготовлены из листовой нержавеющей стали толщиной 0,3 мм и представляют собой сваренные встык кольца. Верхняя кромка каждого кольца срезана под углом 10 градусов по отношению к нижней кромке и отбортована по всей окружности внутрь для приваривания к ней сетки. В свою очередь, сетки привариваются к элементам крепления с напуском в 3—4 мм по диаметру для уплотнения сеткой стыка в месте соединения с цилиндром. При сборке колонки элементы крепления сеток ориентируют относительно друг друга так, как показано на рис. 9, чтобы флегма последовательно стекала с одной сетки на другую. Поскольку сущность ректификации состоит в обмене компонентами между паровой и жидкими фазами, то эффективность этого процесса зависит, в первую очередь, от величины поверхности раздела фаз. С целью её увеличения, пространство в колонке между сетками равномерно заполнены небольшими гофрированными кусками такой же сетки — остатками от раскроя основных сеток.
Диаметр последнего нижнего элемента крепления сетки выдержан таким образом, чтобы он входил в цилиндр с натягом, препятствующим выпадению из цилиндра остальных элементов. Для облегчения демонтажа элементов крепления сеток из колонки каждый из них имеет по четыре монтажных лепестка 3. Для этого в боковой стенке каждого элемента в 4-х местах по окружности делаются надрезы на длину 5 мм на расстоянии 5 мм друг от друга. Полученный таким образом лепесток отгибается внутрь, и позволяет легко извлечь контактный элемент из цилиндра подходящим для этой цели инструментом. В лепесток также упирается инструмент при досылке собранного элемента крепления сетки в корпус колонки.
Наружный диаметр колонки выбран по имеющемуся в распоряжении материалу, но из общих соображений следует, что чем больше диаметр колонки, тем меньшее влияние на протекающие в её центральной части процессы будет оказывать тепловой режим стенок, и тем меньше будет вероятность «захлёбывания» колонки при высоких скоростях перегонки.
В ходе предварительных экспериментов были опробованы колонки тех же габаритов, но с насадкой в виде упомянутых выше колец из нихромовой проволоки и мембранная колонка с 8 шт. горизонтальных мембран, изготовленных из никелевой ленты толщиной 0,2 мм. Отверстия в мембранах пробивались специально заточенным бородком на бруске из плотной древесины. Диаметр отверстий составлял 1,0—1,5 мм. при плотности отверстий примерно 16 шт. на 1см2 поверхности мембраны.
Как и следовало ожидать, колонка с сеточной насадкой при одном и том же орошении показала лучшие результаты. Неплохой результат показала и колонка с мембранами, тем более, что их можно изготовить самостоятельно, тогда как найти тонкую нержавеющую сетку представляется достаточно проблематичным.
Использование сеточной колонки, кроме улучшения качества разделения водно-спиртовой смеси, особенно на завершающих этапах перегонки, когда плотность перегоняемой из куба жидкости приближается к плотности воды, дало ещё один несколько неожиданный результат. Выяснилось, что в сеточной колонке (особенно в её нижней части) скапливается значительное количество сивушных масел, о чём свидетельствует их сильный специфический запах. Поскольку колонка съёмная, то сивушные масла можно легко удалить путём промывки колонки в горячей воде.
Ещё одним достоинством съёмной колонки является возможность сокращения общего времени дробной перегонки за счёт того, что первая перегонка виноматериала, содержащего 10—14% спирта и имеющего высокую плотность, проводится только с одним дефлегматором, а колонка применяется на 2-ой и, если потребуется, 3-ей перегонке.
Необходимо отметить, что проведение второй и последующих перегонок представляется весьма рискованным занятием, если перегонки проводятся на открытом огне газовой горелки, поскольку перегонке подвергается легко воспламеняющаяся жидкость, содержащая 75—85% спирта. Если опасное повышение давления в кубе ещё можно отследить по манометру, а «толчки», приводящие к выбросу содержимого куба, предотвратить применением «кипелок», то внезапное появление трещины в сварном шве приведёт к пожару. Поэтому вторую перегонку необходимо проводить на электроплитке с закрытой спиралью, а лучше всего на индукционной электроплите. Последнее накладывает ограничение на выбор материала для изготовления куба. Например, некоторые сорта нержавеющей стали, а также алюминий и медь для этих целей не подходят.
Также весьма опасным представляется использование стеклянных банок с завинчивающимися крышками в качестве сухопарников. Дело в том, что коэффициент линейного расширения стали, из которой изготавливается крышка, на 25—30% больше коэффициента линейного расширения стекла банки [14]. При нагревании до рабочих температур 95—98ОС затяжка крышки банки неизбежно ослабнет. Этим, к слову сказать, пользуются домохозяйки: для того, чтобы отвинтить туго закрученную крышку, они предварительно на несколько секунд опускают её в кипящую воду. Но, если маринованные огурчики от такой процедуры не пострадают, то самопроизвольное выпадение из крышки банки сухопарника, в которой содержится жидкость с высоким содержанием спиртов, да ещё вблизи от открытого огня — грозит пожаром.
Глава 7. Подготовка виноматериала
Как было отмечено выше, выход спирта напрямую зависит от количества содержащегося в винограде сахара и от того, какая доля набродившего спирта будет потеряна при переходе его в уксус в результате уксусно-кислого брожения. Поэтому сбор винограда нужно проводить при достижении им полной зрелости, при которой виноград имеет максимально сладкий вкус и аромат за счёт накопленных эфирных масел. В перезрелом винограде эти показатели снижаются, и спирт получается низкого качества, без соответствующего аромата. Но в любом случае лучше использовать перезрелый виноград, чем недозрелый. Дело в том, что в клеточных стенках и межклеточном пространстве недозрелых фруктов и ягод содержится больше гетерополисахарида пектина, чем в спелых плодах. Сам по себе пектин весьма полезен для здоровья, в частности, он снижает уровень холестерина в крови и очищает организм от тяжёлых металлов и изотопов с длительным периодом распада [56]. Его широко используют в пищевой промышленности, например, при изготовлении зефира. Но при спиртовом брожении из пектина получается метиловый спирт.
После сбора кисти винограда освобождают от расклёванных птицами ягод и толстых зелёных плодоножек, именуемых в технике гребнями. Если лето было холодным, и виноград плохо вызрел, то по описанной выше причине необходимо срезать невызревшие зеленоватые ягоды с нижней части гроздей. Совершенно недопустимо использовать ягоды с налётом белой плесени или с серой гнилью.
В литературе по виноделию рекомендуется начинать переработку винограда через 4 часа после его сбора, но на практике выдержать такой срок сложно. Как правило, переработка начинается на следующий день, т.е. через 12—15 часов.
Собранный виноград не моют. Вместе с гребнями его основательно раздавливают деревянной толкушкой в эмалированной ёмкости и полученную мезгу перекладывают в ёмкость большего размера — эмалированную, стеклянную или из нержавеющей стали для подбраживания. В процессе подбраживания из мезги выделяется виноградный сок. Ёмкости сверху обвязывают марлей или неплотной тканью, чтобы в мезгу не попадала плодовая мушка — дрозофила. Личинки этой мушки развиваются преимущественно в бродящих жидких средах, и скопление мушек вблизи ёмкостей с виноградной мезгой однозначно указывает на то, что процесс брожения начался. Чтобы предотвратить уксусное скисание и обеспечить возможно больший выход сока, всплывающую при подбраживании мезгу нужно регулярно перемешивать — два-четыре раза в день деревянным вёселком. Вёселко изготавливают из не смолистых сортов дерева (можно из сухих ветвей яблони или груши, которые всегда есть в саду) и тщательно моют в проточной горячей воде после каждого употребления. Если подбраживание ведётся в стеклянной бутыли, то масса вёселка должна быть минимальной — при неосторожном ударе о стенку бутыль легко раскалывается изнутри.
Длительность подбраживания кардинальным образом влияет на качество виноматериала. При недостаточном подбраживании выделяется меньше сока и образуется меньше дрожжей. В результате брожение затянется на лишних полторы-две недели, что ухудшит качество виноматериала. При излишне долгом подбраживании в сусле образуется много дрожжей, которые развариваются при кипячении в кубе аппарата и ухудшают качество дистиллята. Если лето было сухим, тёплым и долгим, а перед сбором винограда не прошли обильные дожди, то оптимальная длительность подбраживания при температуре 19—21оС составляет от 82 до 87 часов. Подбраживание в течение 70 час увеличивает срок брожения с 16 до 24 дней.
По окончании подбраживания из сосуда с мезгой самотёком сливают виноградный сок, который пойдёт на изготовление вина, а оставшуюся мезгу пускают на изготовление виноградной водки. Для этого мезгу заливают тёплой водой в количестве, примерно равном объёму мезги, выдерживают не более двух часов, периодически помешивая, а затем прессуют. При этом совершенно не обязательно использовать прессовое оборудование — достаточно просто отжать мезгу руками. Объём доливаемой в мезгу воды зависит от качества винограда. Если виноград хорошо вызрел и дал насыщенный, ароматный и сладкий сок, то объём воды можно увеличить в 1,5 раза. При большем количестве воды водка утратит характерные вкус и аромат винограда. Разумеется, что водка получится более вкусной и душистой, если для её изготовления смешать виноградный сок с настоем на мезге, или перегнать в спирт только одно виноградное вино, полученное с небольшим количеством добавляемого для крепости сахара. Повторное, с целью экономии, использование виноградных выжимок, т.е. их повторное настаивание и прессование — нежелательно, т.к. на воздухе выжимки быстро и незаметно для глаза плесневеют. Водка из закисших и тем более заплесневелых выжимок будет обладать неприятным запахом и жгучим вкусом.
Поскольку виноградную водку можно получить как перегонкой виноградного вина, так и перегонкой сброженного настоя на виноградной мезге с добавлением сахара, то имеет смысл ознакомиться с основными технологическими приёмами получения виноматериала, как в том, так и в другом случае.