A complex assembly line has many work centers, and each work center consumes one or many components. The components have to be added to build the final product, assuming that hundreds of components are added to complete the final product.
It would be too difficult to keep track of the sequences in which the components are added. You can actually define which component has to be added at which work center to define the sequence of adding the components to the final product.
Let's take the example of Computer Desk. We have three components, and each component is required at a specific work center. You can define which component will be consumed during which operation. Look at the following bill of material configuration, where I have configured which component will be consumed during which operation:
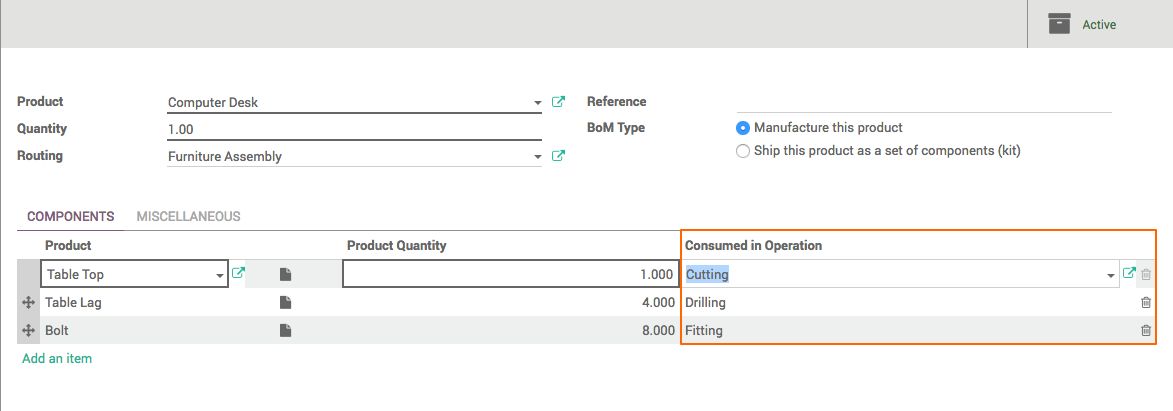
Save the bill of material and you are ready to test the flow in production. Let's create the manufacturing order for one quantity of Computer Desk. Look at the next screen of the manufacturing order that I have created. The components are not available yet. It can be scheduled for production, and the schedule will create the procurement order to purchase the components. Later, it can be started at the work center when the components are available:
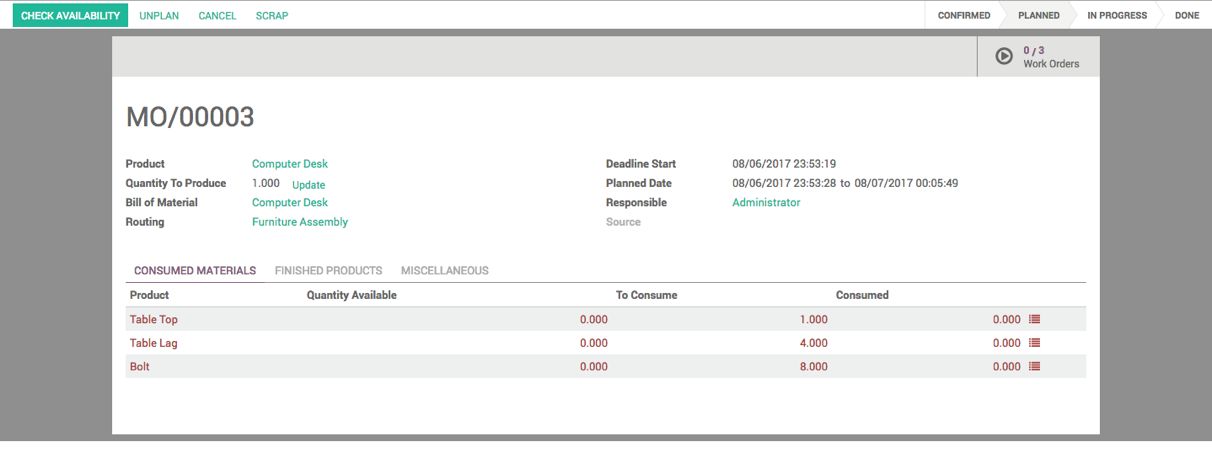
Process the procurement, and receive the components. As soon as the components are received, the manufacturing order will be ready to be produced.
Go to the Cutting work center and open the work order; it will be ready to be worked on as soon as the components are available:
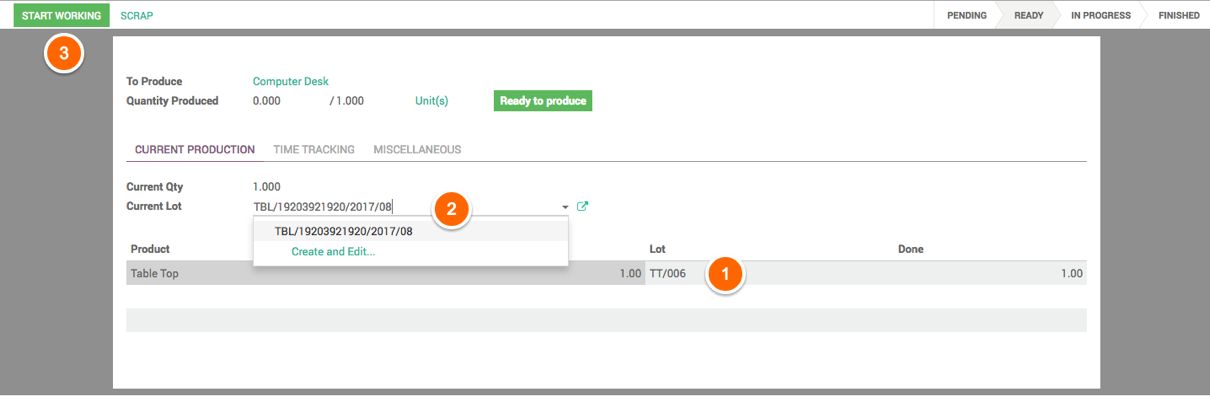
As we have enabled the component consumption at the operation level, we will get the list of components that will be consumed during the Cutting operation. The first step is to select the lot/serial number for the component assigned from the inventory.
The final product is tracked by unique serial number. Please assign a serial number by creating a new serial number. Finally, click on the START WORKING button to start production. You will be asked to select the component by assigning the correct serial or lot number for each operation; complete all the operations.
Complete the manufacturing process in the end by clicking on the MARK AS DONE button. This will also update the quantity of finished products in the inventory.
In the case that work item has more than one quantity, all the quantities can be processed at once if the final product is tracked by the lot number. The Computer Desk is tracked by a unique serial number, so only one quantity can be processed for each operation at a time.
Each time, assign the serial/lot number for the component, create a new serial for the Computer Desk, and start the operation. When you finish the process of one quantity, you will be asked to assign the component and serial number for the next quantity to be produced:
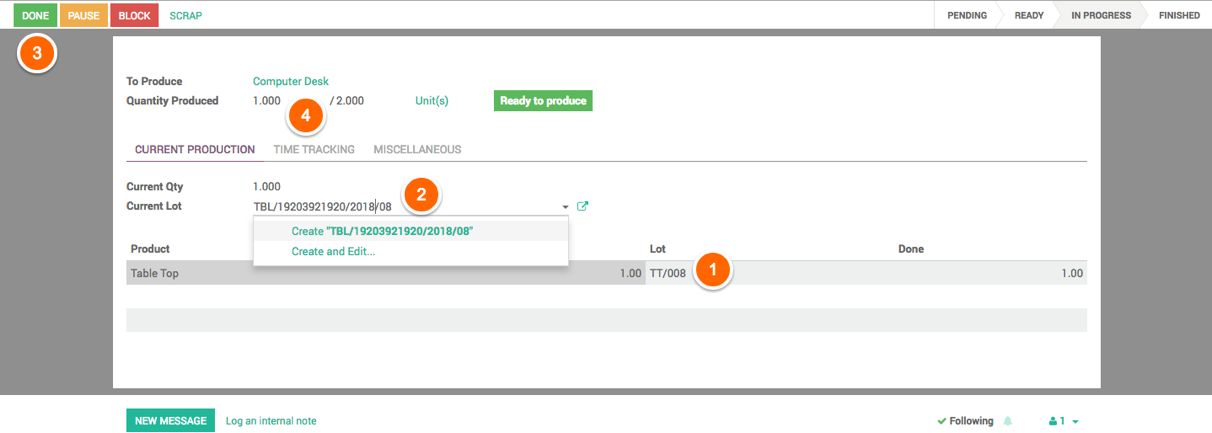
Take a look at the preceding screenshot of an operation where one quantity is already produced. The operation asks you to assign the lot for the Table Top and serial number for the final product to be produced next.