Each business is required to add the operational cost to the cost of the finished product to get the correct cost of the finished product. We have already seen how to compute the cost of a finished product by adding the cost of the components in the Complete the first manufacturing order recipe earlier.
Let's see how to add the operations cost to the cost of the components so that we can have the final cost of the product.
The cost of operations includes the cost of electricity, labor, or any other additional direct or indirect costs incurred to complete the manufacturing operation.
The operations cost can be configured at the work center; you have to derive the Cost per hour for each work center. It includes all the operational Costs per hour for a work center. The following is a screenshot of a Cutting Work Center having a cost of 270 per hour:
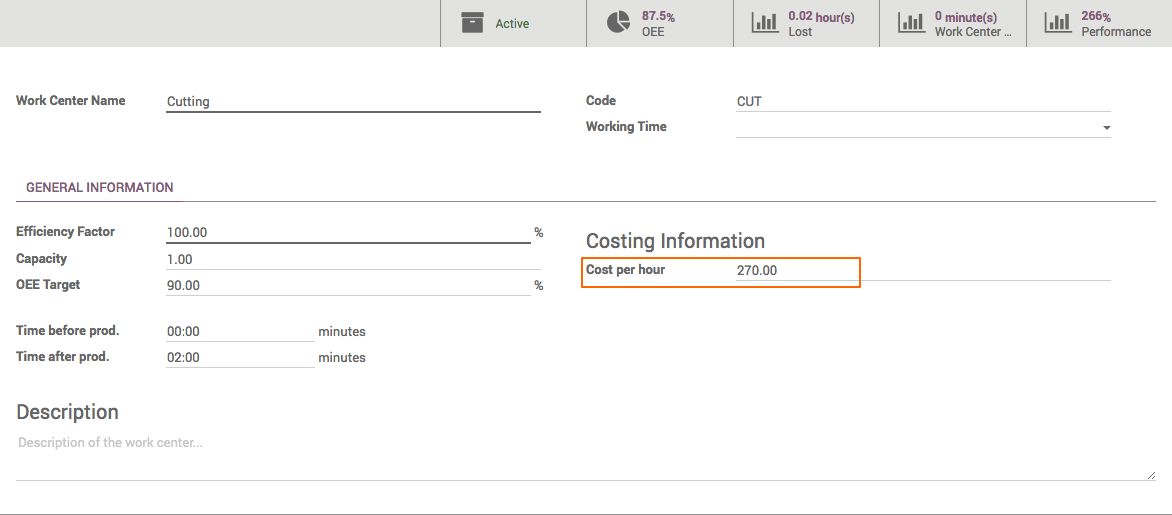
The cost per hour will be used to compute the cost of operations based on the time taken to complete the operation at the work center.
Assume that the costing method for all the components, and the final product, Computer Desk, is set to Real Price. On top of that, we have three work centers each consuming electricity and labor. Based on these costs, we compute the Cost per hour for each work center, as shown in this table:
Number | Work Center | Cost / hour | Duration |
1 | Cutting | 270 | 4:24 |
2 | Drilling | 250 | 00:49 |
3 | Fitting | 460 | 1:02 |
Let's process a manufacturing order which was completed in some minutes. Look at the duration in which Computer Desk was produced in the preceding table. The Cost Analysis report will be generated as soon as you click on the MARK AS DONE button. The following screenshot shows the cost report:
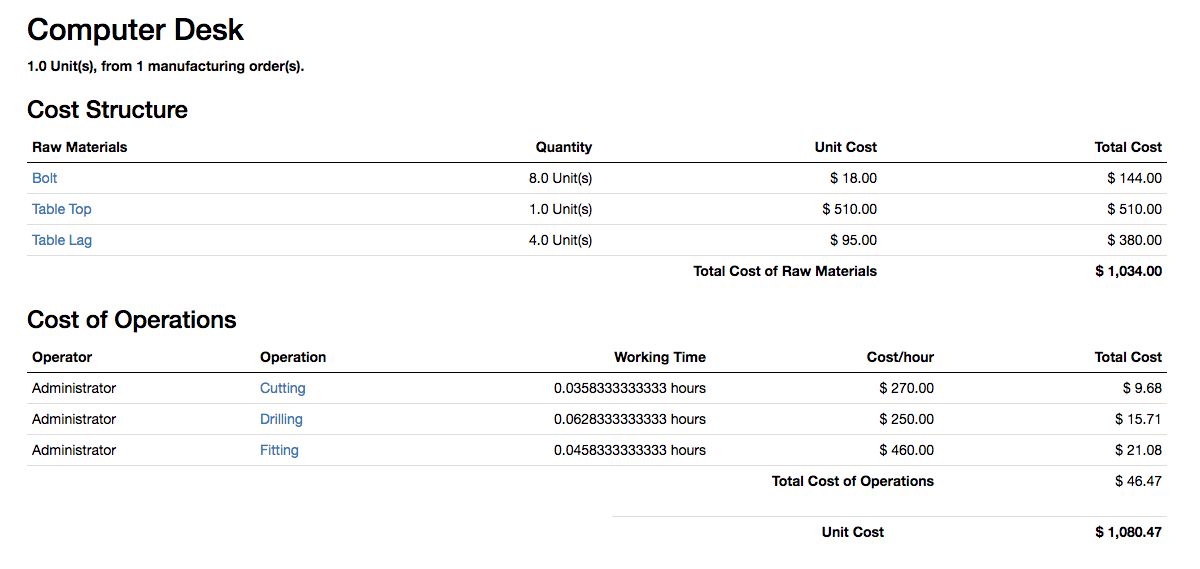
We have two different types of costs listed in the report: the cost of components and the cost of operation depending on the time spent on each operation.
The average cost of Computer Desk produced in our plant can be printed from the Cost Analysis report available on the product form. The total cost of production can be divided by the number of units produced. This will help us achieve the average cost per unit produced in the plant.
Let's take an example of two manufacturing orders. The components are bought at different rates for the two different manufacturing orders, and the operations are performed within different durations at each work center. This is shown in the following table:
Component | Cost Price for MO/00001 | Cost Price for MO/00002 |
Table Top | 490 | 510 |
Table Leg | 100 | 95 |
Bolt | 16 | 18 |
The following report is printed from the Computer Desk product after successfully completing the two manufacturing orders listed earlier:
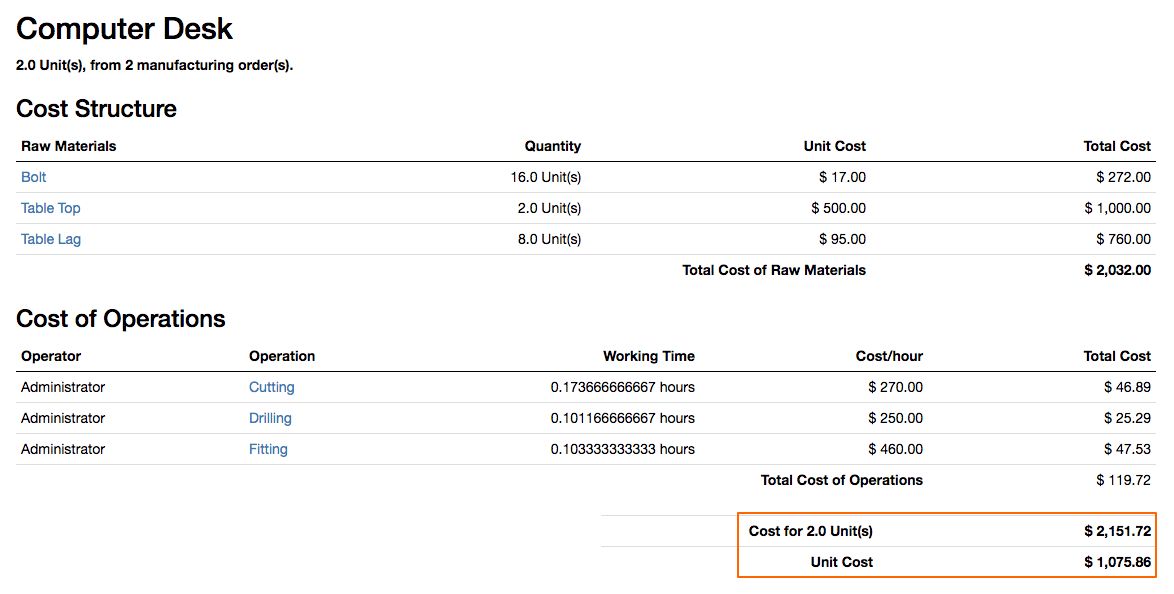
Aside from the Cost Analysis report, but the Inventory Valuation report also includes the cost of Computer Desk as per the costing computed during production. Let's check the Inventory Valuation report under the Inventory application. We will have two Computer Desks having two different values as per the manufacturing cost:

The average cost price will be available in the cost analysis report no matter which costing method is set to compute the costing for the finished product.