Сварочная дуга
Продолжительный электрический разряд, который наблюдается при атмосферном давлении в газовой среде между двумя электродами, называется сварочной дугой. Если она образуется между электродами, роль одного из которых играет металлический или угольный стержень (электрод), а другого – свариваемый металл, тогда такая дуга называется дугой прямого действия. В том случае, если два электрода находятся под некоторым углом относительно друг друга, она называется дугой косвенного действия. Первая применяется в большинстве наиболее распространенных видов сварки, а вторая, будучи менее удобной, – при некоторых специальных видах сварки, например при атомно-водородной. При сочетании обоих видов дуги образуется комбинированная дуга.
Схематическое изображение дуги прямого и косвенного действия показано на рис. 54.
Рис. 54. Схема сварочной дуги: а – прямого действия; б – косвенного действия; 1 – электрод; 2 – газовое облако; 3 – столб дуги; 4 – соединяемая часть; 5 – анодное пятно; 6 – сварочная ванна; 7 – кратер; 8 – катодное пятно
Дуга прямого действия представлена столбом с основанием в углублении, которое возникает на поверхности сварочной ванны. Форма столба дуги бывает цилиндрической или чуть конической. Его верхняя часть контактирует с раскаленным концом электрода. Эта зона называется катодным пятном. Противоположным ему является анодное пятно, образованное основанием столба в зоне его соприкосновения со свариваемым металлом (напомним, что катод заряжен положительно, а анод – отрицательно). Если значение сварочного тока не превышает средних показателей, т. е. составляет примерно 200–300 А, то диаметр катодного пятна приблизительно в 1,5–2 раза меньше анодного.
Столб дуги образует вещество, состоящее из раскаленных и сильно ионизированных газов, которое называется плазмой. В нем сконцентрировано основное количество энергии сварочной дуги, в связи с чем его осевая часть является зоной самой высокой температуры (5500–7800 °C), и она тем выше, чем больше плотность тока в сварочной дуге. Столб дуги окружает ореол пламени (факел дуги). Его образуют пары и газы, температура которых более низкая.
Для возбуждения и горения сварочной дуги необходимы определенные условия. Если рассматривать газы и пары в стандартных условиях, то они оказываются электрически нейтральными и практически не проводят электрический ток. Прохождение последнего через газовую среду возможно только в том случае, если в ней появляются электрически заряженные частицы – электроны, положительные и отрицательные ионы, которые становятся переносчиками электрического тока. (Попутно заметим, что электрон представляет собой материальную частицу, масса которой в 1840 раз меньше массы самого легкого атома – атома водорода, которая несет один отрицательный электрический заряд. Ион – это атом или молекула вещества, может быть либо только положительным, либо только отрицательным.) Такой газ получил название ионизированного. От количества заряженных частиц зависит степень ионизации газа: чем их больше, тем выше степень ионизации, следовательно, и электропроводность газа тоже возрастает.
Процесс ионизации газа наглядно показан на рис. 55, на котором ясно видно, что в результате бомбардировки электрически нейтральных атомов газа (А, А') быстрыми электронами (Э1, Э2), испускаемыми катодом (это явление называется эмиссией электронов), первые теряют один или несколько электронов. При этом их скорость уменьшается, но они продолжают движение к аноду под воздействием его электрического поля. А атомы вместе с электронами, утратившими часть электричества, превращаются в положительно заряженные ионы (+И), которые начинают перемещаться к катоду. При столкновении с ним положительные ионы выбивают из него электроны и частично захватывают их, становясь нейтральными атомами, а остальные электроны движутся к аноду. Отрицательно заряженные ионы (-И) появляются тогда, когда атомы захватывают свободные электроны. Поскольку не все элементы способны на это, отрицательных ионов в ионизированном газе, как правило, меньше, чем положительных.
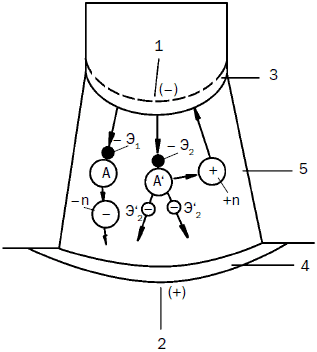
Рис. 55. Схема ионизации газа: I – катод; 2 – анод; 3 – катодное пятно; 4 – анодное пятно; 5 – столб сварочной дуги
Описанный процесс, в ходе которого в среде газа или пара образуются положительно и отрицательно заряженные частицы, называется объемной ионизацией. Кстати, она возможна не только от соударения частиц, ее причиной может быть энергия светового излучения. Кроме того, ионизация газа или пара происходит при их нагревании до температуры 2000 °C (термическая ионизация), когда повышается скорость движения частиц и возрастает число их столкновений.
В сварочной дуге тоже наблюдается процесс образования электрически нейтральных атомов из отрицательно или положительно заряженных частиц, что называется рекомбинацией, а отношение числа заряженных частиц в каком-либо объеме газа к общему их количеству до начала ионизации – степенью ионизации. Образование и распад заряженных частиц в газе при данной температуре сбалансированы, т. е. степень ионизации нагретого газа сохраняется постоянной. При степени ионизации, равной единице, каждая частица в данном объеме газа несет тот или иной заряд. Чем ниже температура, при которой это происходит, тем с большей легкостью в газовой среде образуется дуговой разряд (сварочная дуга).
Степень термической ионизации у различных элементов разная. Легче всего она достигается у калия, натрия и кальция, в связи с чем их наличие в столбе сварочной дуги способствует ее возбуждению и обеспечивает устойчивость ее горения. Поэтому данные вещества всегда добавляются в электродные покрытия.
Кроме того, все элементы обладают разным потенциалом ионизации, т. е. тем количеством энергии, которое требуется затратить, чтобы выбить один электрон из оболочки атома того или иного элемента. Например, потенциал калия, натрия и кальция ниже (приблизительно в 3,4, 2,8 и 2,4 раза соответственно), чем у азота или кислорода. Это дополнительно объясняет их положительное влияние на горение сварочной дуги.
Ионизация газа и образование в нем дугового разряда представляют собой сложные физические процессы, возникновение и протекание которых определяется различными факторами. В частности, для того чтобы катод стал испускать свободные электроны, должны осуществляться следующие процессы:
– термоэлектронная эмиссия, развившаяся под воздействием высокой температуры катода и позволившая электронам покидать его поверхность;
– автоэлектронная эмиссия, являющаяся следствием воздействия электрического поля, которое отрывает свободные электроны от катода;
– эмиссия в результате ударов положительно заряженных ионов по поверхности катода;
– фотоэлектронная эмиссия, являющаяся итогом воздействия световых лучей дугового разряда на катод.
Таким образом, источники пучков заряженных частиц, благодаря которым поддерживается устойчивое горение сварочной дуги, – это эмиссия электронов катодом и объемная ионизация газов.
Теперь необходимо понять, как именно образуется дуга. Весь процесс выглядит следующим образом (рис. 56):
Рис. 56. Схема образования дугового разряда: а – стадия короткого замыкания; б – стадия появления прослойки расплавленного металла; в – стадия формирования шейки; г – стадия возникновения сварочной дуги; 1 – электрод; 2 – основной металл; 3 – дуга
1) при прикосновении концом электрода к основному металлу в сварочной цепи возникает короткое замыкание;
2) электрический ток, отличающийся высокой плотностью в зонах контакта основного металла с электродом (из-за неровности поверхности электрода контакт происходит одновременно в нескольких точках), расплавляет последний, в результате чего появляется тонкая пленка жидкого металла;
3) при некотором отведении электрода из жидкой прослойки металла вытягивается шейка, в которой плотность и температура металла еще более увеличиваются;
4) вследствие испарения металла шейка рвется, а в создавшемся ионизированном облаке газов и паров, образовавшемся между электродом и металлом, загорается сварочная дуга.
В дальнейшем авто– и термоэлектронная эмиссия поддерживают устойчивое горение сварочной дуги при соответствующем токе и напряжении в сварочной цепи.
Напряжение сварочной дуги – это напряжение между электродом и металлом. Его величина определяется длиной дуги. При этом прослеживается такая закономерность: чем короче дуга, тем ниже напряжение, несмотря на то что ток может не меняться. Устойчивое горение сварочной дуги при использовании металлического электрода обеспечивается напряжением 18–28 В, а при применении угольного или графитового электрода необходимое напряжение возрастает до 30–35 В. Напряжение, при котором возникает дуговой разряд, должно быть выше чем то, при котором сварочная дуга поддерживается на соответствующем уровне. Это обусловлено тем, что на первой стадии температура воздушного промежутка недостаточна для того, чтобы сообщить электронам такую скорость, при которой может начаться ионизация атомов газа.
Сварочная дуга бывает:
– устойчивой. Это означает, что она горит равномерно, а произвольные обрывы дуги, для устранения которых необходимо повторное зажигание, отсутствуют;
– неустойчивой. Наличие того, чего нет при устойчивой дуге, изменяет ее характер с точностью до наоборот.
Устойчивость дуги в основном определяется следующими факторами:
– род электрического тока. Он может быть постоянным и переменным;
– состав электродного покрытия. Повысить устойчивость горения сварочной дуги можно с помощью введения в покрытие и флюсы элементов с низким потенциалом ионизации, о которых говорилось ранее;
– полярность. При постоянном токе она бывает прямой и обратной. В первом случае минус источника тока подсоединяется к электроду, а во втором – к изделию. При работе угольным электродом предпочтительнее ток прямой полярности, поскольку при нем дуга легко загорается и отличается устойчивостью. Ток обратной полярности востребован при сварке тонких металлических листов и в других случаях, когда требуется уменьшить выделение тепла;
– длина дуги. Она равна расстоянию от торца электрода до поверхности сварочной ванны. Для стального электрода длина дуги составляет не более 2–4 мм. В этом случае она называется короткой. Для нее характернытакие качества, как устойчивое горение и оптимальное протекание сварочного процесса.
Дуга длиной 4–6 мм считается нормальной, более 6 мм – длинной. В последнем случае отмечается ряд негативных явлений: во-первых, плавление происходит неравномерно, дуга неустойчивая; во-вторых, капли металла, капающие с электрода, могут подвергаться окислению кислородом и насыщению азотом из атмосферного воздуха; в-третьих, наплавленный металл приобретает пористость, а шов – неровную поверхность; в-четвертых, падает производительность, возрастает разбрызгивание жидкого металла, возникают непроваренные участки.
Сварочную дугу можно классифицировать не только по принципу действия (прямого, косвенного и комбинированного), длине, родутока, полярности постоянного тока или виду электрода, но и по таким признакам, как:
– длительность горения. Различаются стационарная и импульсная дуга;
– степень сжатия. Дуга может быть свободной и сжатой;
– характер среды, в которой происходит сварка. Дуга бывает открытой (горение происходит в атмосферном воздухе) или закрытой (если она возникает под флюсом либо в среде защитных газов);
– тип статической вольт-амперной характеристики (так называется зависимость падения напряжения в сварочной дуге от силы тока в условиях постоянной длины дуги).
По этому параметру выделяются дуги с жесткой (падение напряжение не зависит от силы тока), падающей (увеличение силы тока приводит к уменьшению падения напряжения) и возрастающей (напряжение возрастает при увеличении тока)характеристикой.
При сварке вокруг дуги и в металле изделия создаются магнитные поля. Если они несимметричны, тогда под их воздействием дуга отклоняется, затрудняя процесс. Действие магнитных полей, в результате которого дуговой разряд отклоняется, называется магнитным дутьем.
Сила магнитного поля пропорциональна квадрату тока, что объясняет такое явление: магнитное дутье усиливается, если вести сварку с применением постоянного тока силой более 300–400 А, в то время как сварка переменным током протекает с менее выраженным магнитным дутьем. Имеют значение и другие факторы, в частности использование флюса, тонко– и толстопокрытых электродов.
Величина магнитного дутья зависит и от других условий, среди которых следующие:
– нахождение ферримагнитных масс в непосредственной близости от зоны сварки;
– тип сварного соединения;
– наличие зазора между кромками;
– точка подведения электрического тока к изделию (рис. 57) и др.
Рис. 57. Отклонение сварочной дуги вследствие магнитного дутья в зависимости от места подведения тока: а – нормальное положение дуги; б – отклонение дуги в левую сторону; в – отклонение дуги в правую сторону
Поскольку магнитное дутье может создавать трудности при выполнении сварки, для нейтрализации или уменьшения влияния предпринимают соответствующие меры, в частности:
– ведут сварку короткой дугой;
– подводят сварочный ток как можно ближе к дуге;
– варят, наклоняя электрод в сторону действия магнитного дутья, и др.
В процессе сварки плавящийся электродный металл постепенно перетекает в сварочную ванну. Это происходит следующим образом:
1) под воздействием высокой температуры сварочной дуги электродный металл расплавляется, например электроду длиной 450 мм для этого достаточно 1,5–2 минут;
2) в результате действия сил поверхностного натяжения и гравитации жидкий металл электрода принимает форму капли, в основании которой образуется тонкая шейка;
3) шейка капли постепенно утончается, что сопровождается увеличением плотности тока в шейке, и удлиняется вплоть до момента касания поверхности основного металла;
4) касание предшествует короткому замыканию, резкому увеличению тока, разрыву шейки капли и возбуждению дуги между электродом и каплей. В результате давления паров и газов она быстро погружается в расплавленный металл сварочной ванны, разбрызгивая некоторую часть материала, после чего весь процесс повторяется с начала (при ручной дуговой сварке каплями переносятся 95 % металла электрода, а 5 % разбрызгиваются). За 1 секунду с электрода на изделие переносится 20–50 капель приблизительно одинакового размера.
Плавление и перенос металла в сварочной дуге показаны на рис. 58.
Рис. 58. Капельный перенос электродного металла на изделие: а – образование слоя расплавленного металла на конце электрода; б – формирование капли; в – касание капли поверхности сварочной ванны; г – возбуждение новой дуги
Время, в течение которого происходят горение дуги и короткое замыкание, составляет приблизительно 0,02-0,05 секунды. Форма капель и их размер зависят от ряда факторов, к которым относятся:
– сила тяжести и сила поверхностного натяжения. При наложении нижнего шва сила тяжести помогает отрыву капли и переносу электродного металла в сварной шов, а при выполнении потолочного шва, напротив, препятствует;
– состав и толщина электродного покрытия, которое снижает поверхностное натяжение примерно на 20–30 %;
– величина сварочного тока;
– диаметр электрода;
– длина дуги и т. д.
При расплавлении покрытия электрода выделяется значительное количество газов, благодаря которым давление в зоне дуги повышается, что приводит к размельчению капель расплавленного металла. С повышением сварочного тока капли уменьшаются в размере. Перенос металла электрода в сварочную ванну крупными каплями наблюдается при сварке на малых токах с применением тонкопокрытых электродов. При увеличении плотности сварочного тока и применении толстопокрытых электродов перенос электродного металла в сварочную ванну напоминает поток мельчайших капель, которые следуют друг за другом. Поэтому данный процесс называется струйным переносом металла (рис. 59).
Рис. 59. Струйный процесс переноса электродного металла на изделие
При этом снижается выгорание легирующих веществ в сварочной проволоке, а чистота металла шва возрастает. Это основное преимущество струйного переноса электродного металла по сравнению с капельным. Но при использовании штучных электродов это невозможно, поскольку плотность тока на электроде не превышает 10–20 А/мм2.
Количество металла электрода, которое может быть расплавлено за конкретный промежуток времени, вычисляют по формуле:
Gр = Кр х I х t,
где Gр – количество расплавленного электродного металла;
Кр – коэффициент расплавления;
I – величина сварочного тока;
t – время горения сварочной дуги.
Между представленными величинами существует прямо пропорциональная зависимость: чем выше величина тока, чем дольше горит сварочная дуга, тем больше электродного металла будет расплавлено и перенесено. Коэффициент расплавления – это количество расплавленного электродного металла в граммах за 1 час, приходящееся на 1 А сварочного тока. Для стальных электродов этот показатель составляет 8-14 г/А·ч и определяется следующими факторами:
– материал, из которого изготовлен электрод;
– состав электродного покрытия;
– род и полярность тока.
При сварке неизбежны потери жидкого металла, которые возникают в результате разбрызгивания, испарения и окисления кислородом расплавленного металла. Следовательно, в наплавленный металл сварного шва переносится лишь часть металла электрода. Чтобы вычислить количество наплавленного металла, в формуле следует заменить коэффициент расплавления коэффициентом наплавки (Кн), который меньше первого на величину потерь металла электрода, которые составляют 1–3 г/А·ч.
Представленные коэффициенты необходимы для определения расхода электродов, а также для регламентации сварочных работ.